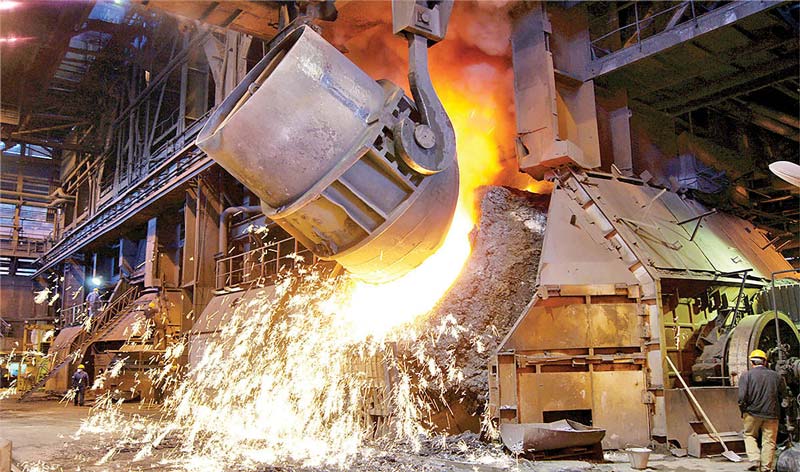
صنعت فولاد در ایران
جمهوری اسلامی ایران با تولید حدود ۳۲ میلیون تن فولاد در سال ۲۰۱۹ و با جهش ۴ رتبهای نسبت به سال ۲۰۱۶ در رتبه دهم دنیا قرار گرفته است. تولید فولاد ایران در سالهای گذشته همواره روند افزایشی داشته و نسبت به ده سال گذشته نیز حدود ۳ برابر شده است! همچنین صنعت فولاد در ایران توانسته علاوه بر تأمین مصرف داخلی، در بین ده کشور صادرکننده فولاد خام نیز قرار گیرد.
بخش فروش داخلی فولاد خام و سایر محصولات فولادی تولید شده در شرکتهای داخلی عمدتا در بورس کالا انجام میشود. علاوه بر تأمین نیاز داخلی، افزایش تولید و فروش صادراتی به جهت تأمین ارز مورد نیاز کشور از محل صادرات غیر نفتی بسیار مورد اهمیت است. لذا پیشبینی میشود که حمایتهای ویژه دولتی از این صنعت در آینده نیز ادامهدار باشد.
به طور کلی میتوان گفت که آینده بازار جهانی فولاد را میتوان مثبت ارزیابی کرد. تولیدکنندگان ایرانی فولاد در صورت اتخاذ استراتژیهای مناسب میتوانند از ظرفیتهای موجود در بازارهای داخلی و خارجی و حمایتهای دولتی استفاده کرده و علاوه بر سودآوری مناسب برای سهامداران، سهم ویژهای در رشد و رونق اقتصادی کشور داشته باشند. پیشبینی میشود که طی سالهای آینده روند تولید فولاد ایران همچنان رو به افزایش بوده و تا سال ۲۰۲۵ به بیش از ۵۰ میلیون تن در سال برسد.
چه کشورهایی مشتریان فولاد ایران هستند؟
کشورهای ASEAN مانندمالزی، سنگاپور، میانمار، تایوان، تایلند، فیلیپین، اندونزی بهطور کلی کشورهای خاور دور آسیا واردکننده اصلی فولاد ایران هستند. پیش از سال ۲۰۱۷، مقداری از صادرات به بازار اروپا تعلق داشت اما به دلایلی بعد از آن ایران بازار اروپا را از دست داد.
مواد اولیه و روش تولید
همانطور که گفته شد فولاد آلیاژی از آهن است که درصد پایینی (بین ۰.۰۲ تا ۲ درصد) کربن و مقادیری از عناصر دیگر با آن ترکیب شده است. لذا مواد اولیه تولید فولاد نیز عمدتاً سنگ آهن، کنسانتره، گندله و کلوخه آهن است. کنسانتره یا خاکه آهن با آسیاب کردن سنگآهن به دست میآید. گندله و کلوخه نیز با استفاده از روشهای خاصی (مثل زینترینگ) در کارخانههای گندلهسازی تولید شده و به عنوان مواد اولیه تولید فولاد به کارخانههای فولادسازی فروخته میشوند. لازم به ذکر است که کارخانههای تولید فولاد عمدتا از کلوخه و گندله و یا قراضه آهن به عنوان ماده اولیه خود استفاده میکنند.
به طور کلی تولید فولاد عمدتاً به دو روش کوره بلند و احیای مستقیم انجام میشود …
- کوره بلند
در روش کوره بلند، گندله آهن به همراه آهک و کُک (نوعی ذغال سنگ) وارد کوره بلند شده و پس از ذوب شدن در دمای بسیار بالا آهن خام به دست میآید. سپس آهن خام در یک مبدل قرار گرفته و کربن اضافی و ناخاصیهای آن گرفته میشود تا فولاد خام تولید گردد. در کشور ما از این روش در شرکت ذوبآهن اصفهان استفاده میشود.
- روش احیای مستقیم
روش احیای مستقیم از دو بخش تولید آهن اسفنجی و سپس ذوب آن در کورههای الکتریکی و با استفاده از جریان بسیار قوی برق تشکیل میشود. در این روش ذرات اکسیدی آهن (سنگ آهن) در تماس با گازهای احیاکننده مثل هیدروژن و مونواکسید کربن در دمای ۷۵۰ تا ۹۰۰ درجه سانتیگراد احیا شده و به آهن اسفنجی تبدیل میشوند. سپس آهن اسفنجی به دست آمده در کورههای الکتریکی بسیار بزرگی قرار گرفته و با استفاده از جریان بالای برق فرآیند ذوب و فولادسازی صورت میگیرد…
از مزایای استفاده از این روش نسبت به کوره بلند عدم نیاز به ذغال سنگ (کُک) به عنوان منبع حرارت و استفاده از جریان برق، کاهش آلودگیهای زیستمحیطی و عدم نیاز به مواد اولیه فرآوری شده (مثل گندله) را میتوان نام برد.
نهایتا پس از طی مراحل فوق و با استفاده از یکی از روشهای کوره بلند یا احیای مستقیم، سنگآهن استخراج شده از معادن تبدیل به شمش فولاد خام شده و برای تولید محصولات بعدی آماده میشود.